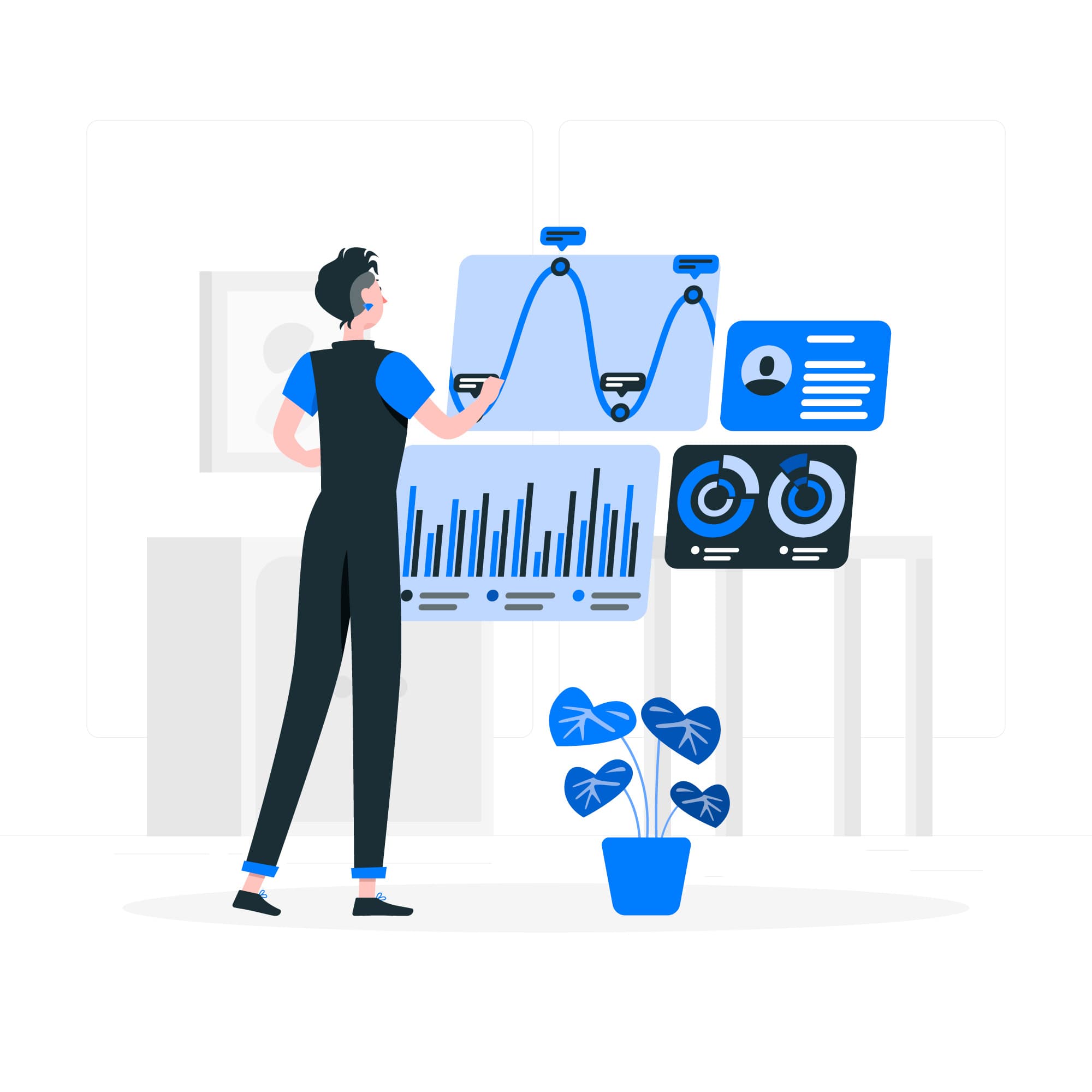
The manufacturing industry stands on the brink of a new era, powered by Artificial Intelligence. One of the most impactful applications of AI in this sector is predictive maintenance (PdM). Traditionally, manufacturers relied on reactive maintenance (fixing things when they break) or preventative maintenance (scheduled check-ups), both of which have significant drawbacks – unexpected downtime and unnecessary servicing, respectively.
What is AI-Powered Predictive Maintenance?
AI-powered Predictive Maintenance leverages sensor data, machine learning algorithms, and advanced analytics to forecast when equipment is likely to fail. Instead of waiting for a breakdown or performing routine maintenance that might not be needed, PdM allows businesses to schedule maintenance precisely when it's required, minimizing disruption and maximizing operational efficiency.
Key AI Technologies Involved:
- IoT Sensors: Collect real-time data on equipment performance, such as temperature, vibration, pressure, and operational speed.
- Data Analytics: Process vast amounts of sensor data to identify patterns and anomalies that may indicate impending failure.
- Machine Learning (ML): Algorithms are trained on historical data to learn failure patterns and predict future issues with increasing accuracy. Techniques like anomaly detection and Remaining Useful Life (RUL) estimation are common.
Transformative Benefits for Manufacturers
Implementing AI-driven predictive maintenance offers a multitude of advantages:
- Reduced Unplanned Downtime: By anticipating failures, manufacturers can schedule repairs during planned shutdowns, drastically reducing costly unexpected interruptions.
- Optimized Maintenance Schedules: Maintenance is performed only when necessary, avoiding over-maintenance and saving resources.
- Extended Equipment Lifespan: Proactive care and addressing minor issues before they escalate can significantly prolong the operational life of machinery.
- Improved Safety: Identifying potential equipment failures early can prevent hazardous situations and improve workplace safety.
- Significant Cost Savings: Reduced downtime, optimized labor, lower spare parts inventory, and fewer catastrophic failures all contribute to substantial cost reductions.
- Enhanced Productivity: With machinery running reliably and efficiently, overall plant productivity increases.
Real-World Applications
Consider a large-scale automotive plant. AI algorithms can monitor robotic arms on the assembly line, analyzing vibration patterns. If an anomaly is detected that suggests a motor is likely to fail within the next 72 hours, maintenance can be scheduled during the next shift change, preventing a costly line stoppage during peak production.
Similarly, in chemical processing, AI can monitor pumps and valves for subtle changes in pressure or flow rate that might indicate an impending leak or blockage, allowing for intervention before a critical failure occurs.
The Future is Predictive
AI-powered predictive maintenance is more than just a trend; it's a fundamental shift in how manufacturers approach asset management and operational reliability. As AI technology continues to advance and become more accessible, its adoption will become a key differentiator for businesses aiming to thrive in the competitive landscape of Industry 4.0.
At AI Automation Co., we specialize in developing and implementing tailored AI predictive maintenance solutions that deliver tangible results. Contact us to explore how we can help your manufacturing operations achieve new levels of efficiency and resilience.